Définir la distribution d'un entrepôt est la première étape du travail de conception de l'installation. La répartition de l'espace peu sembler simple mais, dans la pratique, cet élément peut s'avérer complexe. Cet article aborde les principaux facteurs qu'il est nécessaire de prendre en compte et propose l'exemple d'un layout d'entrepôt en six zones différentes.
En général, le concepteur d’un entrepôt doit tenir compte de certains facteurs qui limitent considérablement la surface disponible. C’est pourquoi la distribution doit être soigneusement étudiée. Pour déterminer la disposition interne et externe d’un entrepôt, trois situations différentes peuvent se présenter et conditionner l’affectation des espaces : installation de nouveaux entrepôts, agrandissement d’entrepôts existants ou réorganisation d’entrepôts déjà en service. La dernière de ces trois situations n’implique pas la prise de décisions cruciales susceptibles d’affecter le développement de l’entreprise à moyen et long terme.
Toutefois, quelle que soit la situation, la distribution générale d’une installation doit aller de pair avec un bon système de stockage, autrement dit avec un système couvrant les besoins suivants :
- L'exploitation optimale de l’espace
- Une manipulation des marchandises réduite au minimum
- Une facilité d’accès au produit stocké
- Le meilleur taux de rotation possible
- Une flexibilité maximale de mise en place du produit
- Un contrôle des quantités stockées simplifié
Pour atteindre ces objectifs, il faut tout d’abord effectuer une distribution planimétrique, c’est-à-dire le plan d’aménagement de l’entrepôt.
Le plan de distribution doit être réalisé en respectant avant tout les règles élémentaires de stockage déjà citées : éviter les zones et les points de congestion, faciliter les tâches de maintenance et déterminer les moyens nécessaires pour obtenir la plus grande vitesse de mouvement possible et la réduction des temps de travail.
Dans la conception de la distribution, les zones suivantes doivent être parfaitement définies :
A. Zones de chargement et déchargement
B. Zone de réception
C. Zone de stockage
D. Zone de préparation des commandes
E. Zone d'expédition
Un exemple de distribution pour laquelle toutes ces zones ont été prévues :
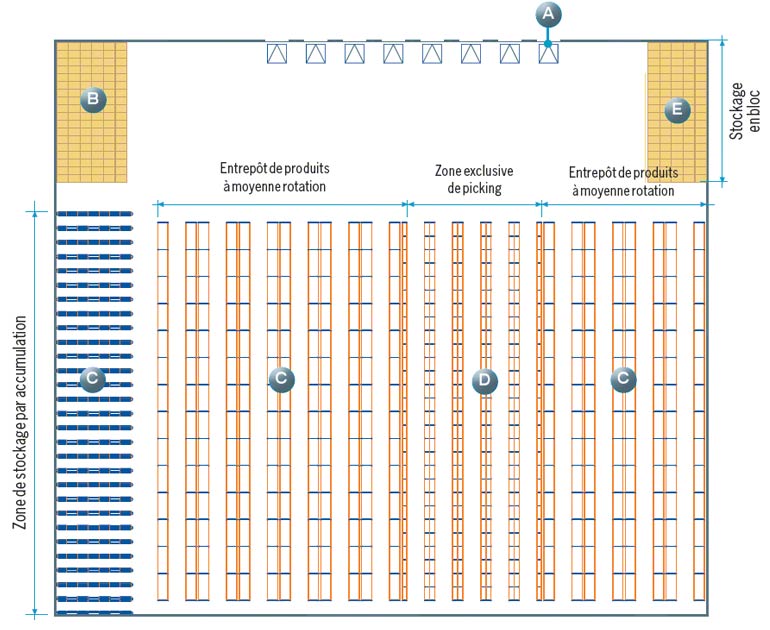
Exemple de distribution d’entrepôt où toutes les zones sont prises en compte
Zones de chargement et de déchargement (A)
Les camions, ou les véhicules de transport et de livraison des marchandises, ont un accès direct aux zones de chargement et de déchargement généralement situées à l’extérieur de l’entrepôt, ou intégrées à celui-ci.
Dans un entrepôt bien organisé, ces activités doivent être séparées du reste de l’installation en aménageant un espace suffisant pour le chargement et le déchargement. Cette zone peut être intégrée à l’entrepôt ou être indépendante.
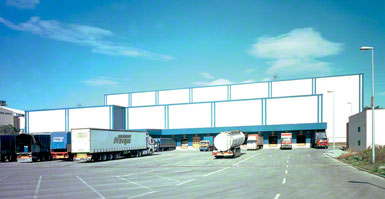
Quai avec plate-forme adossée à un entrepôt.
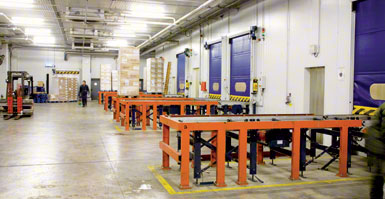
Quai avec plate-forme intermédiaire dans un entrepôt frigorifique.
Zones de chargement et déchargement intégrées à l'entrepôt
Si les zones destinées au chargement et au déchargement sont construites directement sur les côtés de l’entrepôt, afin de pouvoir procéder aux opérations sans avoir à faire de détours, elles sont intégrées à l’installation. Le principal avantage est l'obtention d'une plus grande vitesse de manutention du chargement, c’est pourquoi cette modalité est préférable aux options non intégrées, à condition de disposer de l’espace suffisant.
Les camions se garent devant des quais qui peuvent être soit séparés du bâtiment par une plate-forme, soit aménagés sur celle-ci avec une porte d’accès.
- Les quais séparés par une plate-forme intermédiaire sont indiqués lorsque la nature de la marchandise, la préservation de l’environnement interne ou la sécurité du matériel stocké, le recommande. Les entrepôts frigorifiques, dans lesquels il faut éviter à tout prix la perte de frigories que pourrait entraîner l’ouverture d’une porte d’accès sur le quai, sont un exemple d’application caractéristique de quais séparés. Toutefois, cette conception est préférable dans nombre de circonstances, en particulier lorsque la sécurité de l’entrepôt est en jeu.
- Les quais encastrés dans l’entrepôt permettent aux camions d’accoster directement contre le mur du bâtiment. Pour éviter de modifier la température interne de l’installation, leurs portes d’accès doivent être équipées au minimum d’un système de fermeture hermétique. Ce système peut être métallique ou à soufflet de protection.
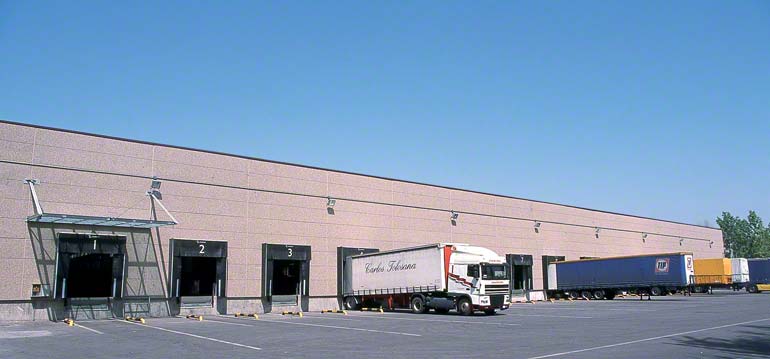
Quai avec accès direct à l'intérieur de l'entrepôt.
Les accès à fermeture métallique sont pourvus d’un système manuel ou automatique qui commande une barrière ; soit fixe, repliable ou enroulable (voir l’illustration ci-contre). Elle s’ouvre lorsqu’un camion accoste et se referme lorsque le véhicule a terminé l’opération. La préservation de la température interne est plus efficace si le système de fermeture est automatique. Outre la fermeture métallique, les portes à soufflet de protection sont pourvues d’un sas qui s’ajuste au camion lorsqu’il est garé devant l’entrée, de manière à préserver le plus possible l’atmosphère interne de l’atmosphère externe.

Porte à soufflet de protection.
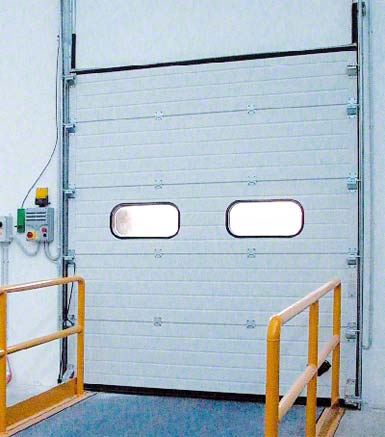
Porte sectionnelle.
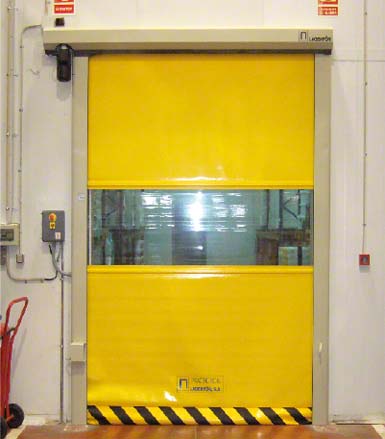
Porte enroulable.
Lors de la conception de ce type de zones de chargement, il est conseillé de prévoir de surélever le sol de l’entrepôt par rapport au niveau de circulation des camions. Il est également possible de concevoir des zones de chargement et de déchargement où les camions entrent dans une fosse, mais le mouvement et les opérations sont plus rapides si le sol de l’entrepôt est surélevé.
La différence de niveau peut être obtenue de diverses façons, c’est pourquoi il n’est pas indispensable de surélever le sol du bâtiment. On peut par exemple abaisser le niveau de la zone de circulation de camions en créant une pente progressive, évitant ainsi les rampes prononcées qui gênent les manœuvres et retardent les mouvements.

Vue d'un quai en fosse.
Pour déterminer cette différence de niveau, deux cas peuvent se présenter, selon le fait les zones de chargement et de déchargement, où les camions sont amenés à accéder, appartiennent ou non à l’entreprise :
- Si les zones de chargement et de déchargement ne sont desservies que par des camions de l’entreprise ayant tous la même auteur de caisse, la différence de niveau peut être précisément fixée.
- En revanche, si elles sont desservies par des camions appartenant à d’autres entreprises, provenant de différents pays et présentant par conséquent différentes hauteurs de caisse, l’installation doit être pourvue d’un système permettant d’ajuster l’écart de niveau.
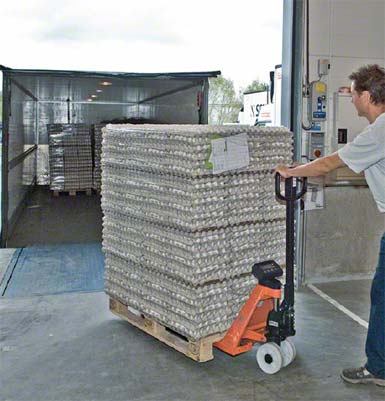
Transpalette.
Il est en général indispensable de disposer d’un système d’ajustage car même si l’on utilise sa propre flotte, et qu’en théorie il n’y a pas d’écart entre les véhicules et le quai, dans la pratique, cette différence existe toujours.
L’une des raisons est que la suspension des camions s’affaisse avec le temps, que la hauteur varie d’un chargement à l’autre ou, le plus souvent, que l’essor de l’entreprise contraint à acheter ou louer d’autres camions. En définitive, la diversité de hauteur de caisse des véhicules est inévitable.
Pour compenser ces différences de niveau, il existe des moyens mécaniques ou hydrauliques. Les premiers reposent sur l’utilisation de ponts ou de passerelles, généralement métalliques, et posés manuellement entre le quai et le camion, comme le montrent les illustrations suivantes. Ces éléments ont pour but de permettre aux chariots élévateurs, aux transpalettes ou tout autre moyen mécanique utilisé pour le chargement et le déchargement des camions, d’entrer et de sortir du véhicule.
Autre option, l’utilisation du second système constitué par une plate-forme métallique, pourvue d’un ou de plusieurs vérins hydrauliques. Cet élément facilite l’accès à la manière d’une rampe – lorsqu’il est intégré au quai – ou élève et abaisse le camion. L’illustration de gauche montre la seconde option, avec plate-forme intégrée au quai.

Passerelle individuelle.
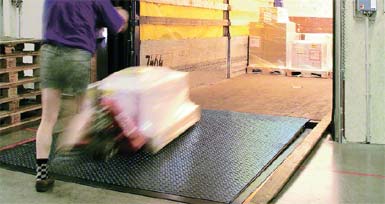
Passerelle intégrée.
Zones de chargement et déchargement indépendantes
Ces zones sont entièrement indépendantes de l’entrepôt, et situées à l'extérieur, mais sont cependant toujours à proximité. Généralement, elles sont formées par une grande esplanade à laquelle les camions accèdent directement. Les véhicules sont garés de façon à pouvoir être chargés ou déchargés au moyen de chariots élévateurs.
Les zones de chargement et déchargement indépendantes sont situées dans les entrepôts qui assurent une seule des deux fonctions. Elles permettent de réduire le temps de mise à quai et augmentent ainsi la vitesse de manutention. En outre, le processus de chargement et de déchargement de la marchandise est ainsi entièrement indépendant du cycle de travail de l’entrepôt.
Dans ces zones, les opérations de manutention de la marchandise dans les camions peuvent être réalisées sur le côté ou par l’arrière du véhicule. Si la manutention est effectuée sur le côté, on utilise des chariots élévateurs, comme le montre l’illustration ci-contre.
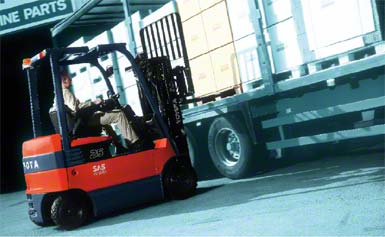
Charriot effectuant la manutention de la marchandise sur le côté.
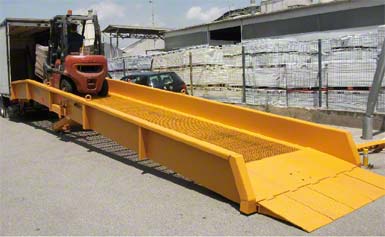
Accès par rampe.
Si au contraire l’opération s’effectue par l’arrière du camion, elle peut être exécutée de deux manières.
La première consiste à accéder au camion avec des chariots, par des rampes. Celles-ci sont habituellement métalliques et s’ajustent au camion, manuellement ou mécaniquement. Il en existe une grande variété sur le marché, mais les plus employées sont les rampes modulaires et les rampes adossées aux quais de déchargement.
Les rampes modulaires sont des structures métalliques pourvues d’une surface de roulement antidérapante, qui peut être fixe – lorsque les camions ont la même hauteur – ou mobile pour les véhicules de différentes hauteurs
D'autre part, les rampes adossées aux quais de déchargement sont construites en briques ou en béton et peuvent également avoir une hauteur fixe ou variable ; dans ce dernier cas, leur construction est similaire à celle des quais de chargement et de déchargement intégrés déjà décrits ci-dessus. La seconde option pour réaliser le chargement et le déchargement des camions par l’arrière est d’utiliser des chemins de roulement mécaniques. Avec ce système, il n’est pas nécessaire d’accéder à l’intérieur de la caisse du véhicule pour effectuer les opérations, il suffit d’installer des chemins de roulement qui permettent à la marchandise de glisser à l’intérieur du camion, le mouvement étant effectué par la poussée des chargements les uns sur les autres.
Charge automatique par chemins de roulement.
L’opération commence par le dépôt d’une ou plusieurs unités de charge à l’entrée du véhicule, lesquelles sont poussées à l’aide d’un second lot d’unités déposées à la position qu’occupait le premier lot. Ainsi les unités de charge s’accumulent jusqu’à ce que la caisse du camion soit remplie.
Zone de réception (B)
La zone de réception doit être aussi indépendante que possible du reste de l’entrepôt afin de pouvoir y réceptionner la marchandise mais aussi en contrôler la qualité et la trier.
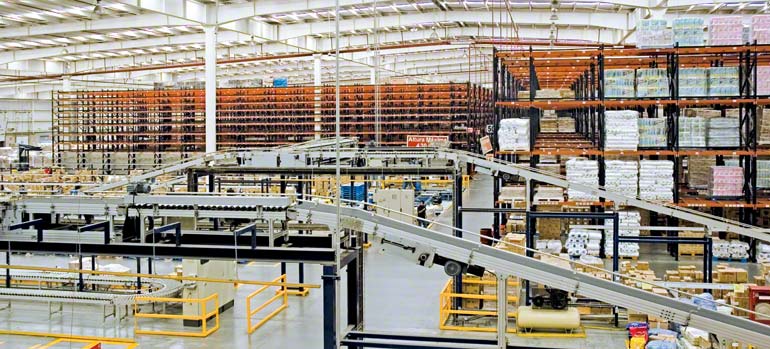
Zone de réception
Après avoir vérifié que la marchandise réceptionnée correspond aux caractéristiques et à la qualité demandée, l’emplacement pour stocker la charge dans l’entrepôt doit être déterminé.
Selon le type d’entrepôt, une transformation des unités reçues peut être nécessaire, dans ce cas, la zone de réception doit être dimensionnée de façon à permettre l’exécution de cette tâche. Il peut être nécessaire, par exemple, de décomposer les palettes entrantes en unités plus petites, ou d’extraire des pièces livrées cerclées, etc.
Compte tenu de la répercussion que peuvent avoir un contrôle bien exécuté et, surtout, une mise en place appropriée sur le rendement futur de l’entrepôt, cette zone doit être aussi spacieuse et indépendante que possible.
Actuellement, la quasi-totalité des produits manutentionnés dans un entrepôt sont pourvus de codes-barres qui peuvent être lus par un scanner. Ainsi, une fois que l’ordinateur central de l’entrepôt a identifié des unités, il peut immédiatement émettre l’étiquette de stockage de la marchandise. Cette étiquette peut être ensuite lue par un cariste ou par les scanners des systèmes mécaniques automatiques dont l’entrepôt est équipé pour déposer la marchandise à l’emplacement voulu.
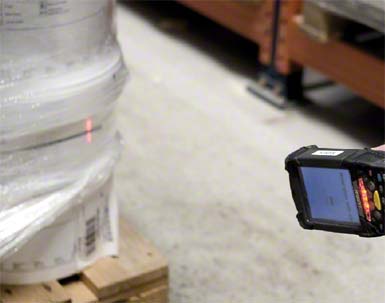
Le terminal de radiofréquence lit l'information codifiée de la palette.
Zone de stockage (C)
Cette zone est uniquement destinée au stockage de la marchandise. Il existe différents modes de stockage :
- Directement sur le sol.
- Directement sur le sol, empilée et en blocs .
- Sur rayonnages.
Le choix du mode dépend surtout du type de produit à stocker, de sa capacité d’empilage ou de sa quantité, et du temps qu’il doit passer dans l’entrepôt.
Le stockage en piles
Le stockage en piles est réalisé en déposant des unités de charge les unes sur les autres sans autre élément intermédiaire que la palette qui leur sert de support. Il a pour avantage de mieux exploiter l’espace, car tous les emplacements sont utilisés. Tous les matériaux ne peuvent pas être stockés ainsi et il ne faut pas oublier que même les marchandises qui le permettent ont un seuil de résistance et, par conséquent, une hauteur maximale d’empilage. L’inconvénient majeur de ce système est qu’il ne permet aucune accessibilité puisque pour prélever une unité de charge, il faut démonter la pile qui la surmonte.
L’empilage peut être principalement utilisé avec deux types d’unités de charge, celles qui pré- sentent une grande résistance interne et celles qui sont conditionnées dans un emballage rigide.
- Les marchandises qui possèdent une grande résistance interne, par exemple les briques, les blocs de béton, etc., permettent un stockage direct, quelquefois même sans palette ni autre systè- me de support. D’autres marchandises, telles que les aliments pour animaux, ciments et granulats stockés en sacs, permettent également ce mode de stockage grâce à leur résistance à la compression, même si des palettes ou d’autres systèmes de support sont nécessaires pour les manutentionner correctement.
- Les emballages rigides, tels que les caisses en carton, en bois ou en plastique, peuvent être empilés sans problème, leur rigidité et leur résistance déterminent le nombre d’unités à empiler sur une hauteur plus ou moins grande
Lorsque la nécessité de stockage en hauteur dépasse la capacité de résistance à l’empilage des unités de charge ou quand une meilleure accessibilité est nécessaire pour la disponibilité du produit, l’utilisation de rayonnages s’impose.
Le stockage sur rayonnages
Le stockage sur rayonnages fait appel à des structures métalliques essentiellement composées d’échelles et de lisses dûment entretoisées. Cette structure multicellulaire forme des alvéoles dans lesquelles sont déposées les unités de charge. La configuration et la disposition des cellules (ou alvéoles) peuvent varier pour s’adapter à différents modes opératoires et besoins d’accessibilité et d’accumulation de la charge .
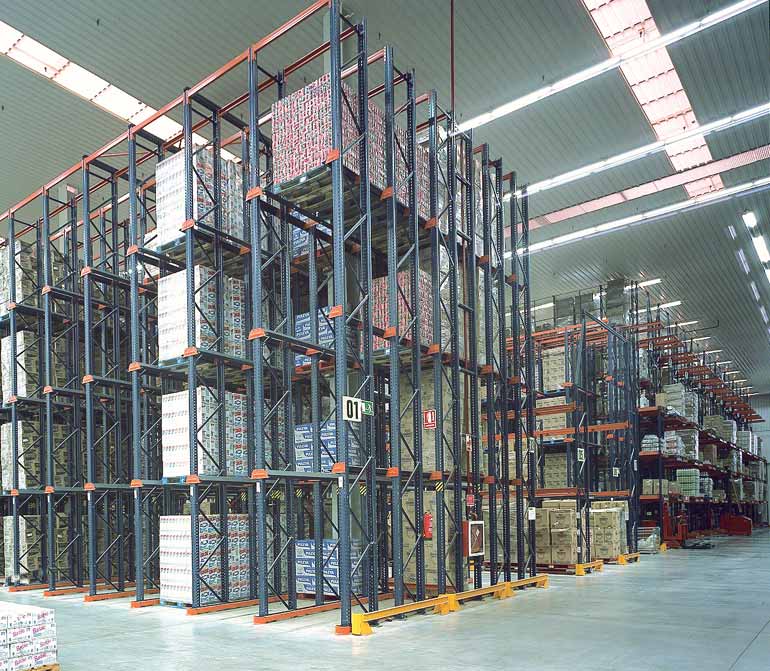
Entrepôt d'une société de distribution.
Zones de préparation de commandes (D)
Les zones que nous allons voir à présent ne sont indispensables que dans les entrepôts où la marchandise subit une modification ou une transformation entre l’entrée et la sortie.
Les zones de préparation de commandes peuvent être intégrées aux zones de stockage. Tel est le cas du picking sur rayonnage. Elles peuvent également être séparées des zones de stockage, par l’aménagement de zones spécifiques généralement équipées de systèmes automatiques ou semi-automatiques.
Zone de préparation de commandes d'un entrepôt de robinetterie et d'accessoires.
Zones d'expédition (E)
Ces zones sont destinées à l’emballage des commandes préparées dans les zones décrites ci-dessus. Que cette opération soit nécessaire ou non, cette zone peut également être destinée à l’accumulation des marchandises à expédier en attente de charge sur les véhicules de livraison ou de distribution.
Pour une vitesse de mouvement appropriée à l’intérieur de l’entrepôt, ces espaces doivent être situés dans un lieu spécifique et différencié du reste de l’installation.
Si des zones de réception et d’expédition séparées ont été aménagées, celles-ci doivent également disposer de zones de chargement et de déchargement. En revanche, si la réception et l’expédition sont proches l’une de l’autre, il suffit d’aménager un seul espace de chargement et de déchargement ; cette option implique néanmoins une plus grande difficulté de contrôle du flux de marchandises et du mouvement de véhicules.
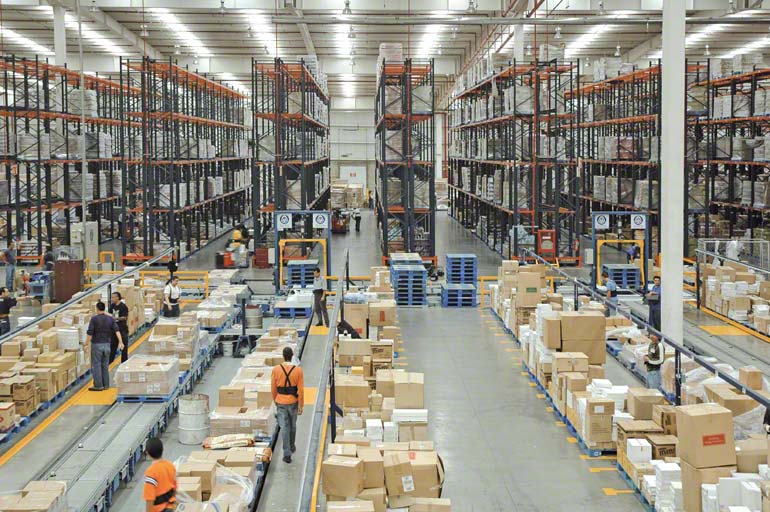
Entrepôt pour une entreprise de distribution.
Zones de services (F)
Une partie de l’entrepôt doit être destinée à certaines activités des services de l’installation, notamment les services généraux et le bureau de contrôle, les vestiaires, les sanitaires et le local de recharge des batteries des engins de manutention.
- L’idéal est de situer le bureau de contrôle entre les zones de réception et d’expédition afin d’accroître le rendement et l’efficacité du personnel.
- Les vestiaires, les toilettes et les services généraux peuvent être installés n’importe où dans l’entrepôt mais le plus logique est de les placer à proximité des bureaux de contrôle. Pour rapprocher ces ressources, une solution consiste à installer ces locaux sur une plate-forme construite au-dessus de la zone de réception et d’expédition.
- Enfin, le local de recharge des batteries des engins de manutention doit être isolé et bien aéré, pour des raisons de sécurité et pour éviter tout incident lors des opérations effectuées dans cette zone.
Chez Mecalux nous sommes conscients du fait que réaliser une distribution correcte est essentiel pour la gestion des flux de marchandises, comme pour la sécurité des opérateurs et des produits. Aussi, c’est pour cela que nous mettons l’accent sur l’importance de cette étape du processus de planification de l’entrepôt, et accompagnons les entreprises pas à pas, afin de réaliser l’agencement idéal, s’adaptant à tous ses besoins actuels et futurs !
Découvrez plus en détail nos services logistiques avec nos consultants.